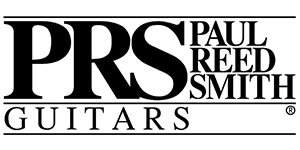
Paul Reed Smith is a perfectionist and dreamer who created a company that turned the guitar manufacturing business upside down. Guitars made by PRS are famous for their impeccable quality and high price tag but this doesn’t stop them from competing (quite successfully though) with such giants of the guitar industry as Fender and Gibson.
Subsidiaries and trademarks:
PRS SE, PRS S2.
Brief history:
Smith, the owner of PRS started making guitars while still a teenager. There is no special education for the entrepreneur. His father played in a jazz band, but earned a living teaching maths, so Paul didn’t have the money to buy first-class instruments. He said that he could get them only if he assembled them himself. Due to insufficient diligence during his studies Paul was expelled from college and, choosing his occupation, mastered the carpentry. That’s how he started to make guitar bodies.
Not playing but “pulling strings” is what he was the best at. "If I played guitar, people would run. If I opened the case of a guitar I'd built, people would gather in a crowd," he recalls. He was looking for buyers among touring artists. It took 10 years to turn the handicraft production into a business. On average, only one in 10 musicians, to whom Paul demonstrated his guitars, made an order. Each instrument took about a month of work.
Eventually having trained, the young master made several models of guitars that he would like to release – he went on a journey along the East Coast looking for potential buyers. Returning home with some money (some part of which was borrowed from friends) Paul Smith established PRS Guitars company (1985). The company was based on pure enthusiasm - the start-up capital appeared thanks to each and every employee who took part in founding.
In 2000 the company's revenue reached $14 million, in 2001 - $21.5 million. Smith focused on high-end electric and acoustic guitars. The average retail price of a guitar from Paul Smith was $3000, the price of limited edition models could reach $60000. It’s no surprise that PRS Guitars has become a favorite brand of many rock and folk stars including Carlos Santana and Al Di Meola. PRS guitars made of mahogany and maple, dried in a special chamber up to 6% humidity, five times polished and covered with eight ultra-thin layers of varnish. The company uses its own pickups. In 2013 25000 instruments - the so-called "Student Edition" priced at $700 a piece - were manufactured by partners in South Korea, but even "SE" shows the high quality inherent in any of the PRS guitars.
Smith was lucky when in 1975 he took a guitar and made his way to the dressing room of Ted Nugent telling the rock musician: "If you don't fall in love with the guitar, you get your money back." Nugent still owns that guitar. In 1980 thanks to the same trick Smith became friends with Carlos Santana. Support of the famous musician, who called PRS a Ferrari in the world of guitars, helped Smith to make a name among musicians. And among well-known vendors, such as Rudi Penza. He first met Smith in the late 1970s, when he came to the Music Shop in Manhattan with several guitars. "I looked at the quality, I said, 'My God, this looks good, and they play great,'" says Pensa, who annually sells 40-50 PRS guitars in his two stores in New York and keeps several copies in his own collection. He says that when you play this guitar, you get a feeling like you’re holding Stradivari violin.
Paul Smith aspires to maintain this feeling. "It takes 10,000 hours to get good at anything. I think it took me 40,000," he laughs. Ted McCarty, the former president of Gibson, has consulted Smith for 12 years on bridge design and the electric pickup circuitry. The owner of PRS Guitars assures that about 80% of its employees are quite decent musicians. And the motivation program is quite appropriate as well - discounts when buying brand guitars, parties, music festivals. But he is a demanding boss. "When Paul spoke, everyone listened," says a former employee who worked as a hand sander at PRS. "You definitely knew when he was in the building, and you definitely watched your ass."
Since such a guitar is a luxury item, the economic crisis hit PRS painfully enough. In 2009 sales dropped by 12%. "I bought my house when the bottom fell out in 2008, and it was worth two-thirds what I paid for it the next day," Smith sighs. A large pile of pre-orders helped the company cope with the difficulties, and in 2010 PRS revenue increased by 30%. "I never worked harder in my life." "Things are better now, but they ain't great," says Smith.
The situation improved with the acquisition of Headline Music. Gavin Mortimer, a founder and CEO of Headline Music who has been selling PRS guitars since 1999, claims that new orders from European retailers continue to increase. Buyers in England often travel 500 km from home to the store just for the sake of buying PRS.
Smith prefers to treat his work as elation. "Love is the fundamental core of doing a good job," he says over the phone while waiting to meet with fans at a music shop near Boston. "I can't ask people to love their work when they come to PRS. But if you want to get that thing sanded perfectly, you're going to have to love it."
Technical and technological achievements:
Pieces from Paul Smith’s interviews
What are the factors and vision affecting product line choices?
I'll give you one example: So we went from Custom 24s to Custom 22s and what was driving it was that almost all artists were playing 22 fret guitars, not 24 fret guitars and we were getting ready to release the Dragon. We changed it over from a 24 fret guitar to a 22 fret guitar at my kitchen table. Ralph and I were talking about it and it ended up becoming the McCarty and the Dragons and we started making 22 fret guitars. We moved the bridge. We moved the neck pickup. We changed the thickness of the guitar and some other things. Thing is, that was all driven by the fact that almost nobody was playing 24 fret guitars.
513 came about when I thought that we might be able to get a pile more tones out of a guitar. You could have a heavy humbucker guitar, a light humbucker guitar, and a single coil guitar all in the same guitar: five pickups and 13 sounds. It was driven by a need to have an extraordinarily sophisticated Swiss Army knife that could do anything.
There's a lot of concern about sustainable materials in the guitar industry. How do you manage your supply chain to avoid legal issues like Gibson and are there any synthetic materials that you would consider using?
The forests in America are in better shape today than they were in 1900. The curly maple thing I'm okay with. It's fine. Mahogany stuff that we've been doing, we're making sure is from sustainable practices. If you take only one seed tree out of an acre, it's fine. You leave seed trees in every acre and they're *very* *very* careful with that. As far as the Indian rosewood, those are trees that blow down in monsoons and are laying on the ground. The collect them and bring them to this place in a tiger reserve. I've been there and people buy these blow-downs. Would you rather rot it or make guitars out of it? It seems okay to me.
These days, a lot of premium guitar brands are using stainless frets. Is there a possibility of PRS offering stainless frets or is that something you just don't want to do?
Stainless steel is mostly made out of nickel. Fret wire is made out of nickel. There's no silver in "German silver". Making frets out of nickel is good. We make our frets really hard so you don't have to refret. Most people are using much softer wire than we are and the strings are so high in hardness so the strings wear the frets away. I've spent a boatload of time trying to get the guitars to sound right. I'm not opposed to stainless steel frets in any way but I don't know enough about it to make a shift right now.
***
We're in a commodity market peddling a quality product. Normally, in a commodity market, you peddle a commodity product, but we decided, in the price range for the SE, to try and do it right instead of having it only look right. I've seen Carlos [Santana] take one out of a box, play it onstage, and be completely happy. I've seen Mark Tremonti [Creed] do the same thing. Dave [Baksh] from Sum 41 plays them onstage [too]. It's a real guitar. And I think it takes the market a long time to get used to something new—it always has. What's new is that, for that money, you can get a guitar that you can make a living on. That's how I divide guitars up—you can have the worst piece of junk ever made and the best guitar ever made. Take Pat Metheny's guitar—something you could make a living on—all the way down to something you couldn't make a living on. At some point, it becomes a musical instrument. We're trying to make stuff that's in that range that you could make a living on.
There was one Nashville NAMM when the entire industry came up and said, "Well, you're now part of the three." Everyone said it. What used to be Fender, Gibson, and maybe a little bit Ibanez—now, it's Fender, Gibson, and PRS. The whole industry—that's what came out of their mouths. "Fender, Gibson, PRS."