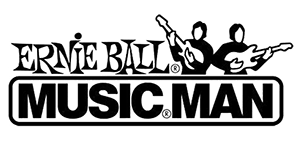
Originally associated with Leo Fender, today the American guitars "Music Man" are among the main alternatives to the "big 2" represented by the brands "Fender" and "Gibson". The great difference between Ernie Ball Music Man and other companies is in the approach to musicians. The company doesn’t try to win everyone’s recognition among guitarists, on the contrary, it tries to make the instruments win their place among guitarists. "Ernie Ball Music Man" is proud of the fact that very often guitarists come to the shop to give their master classes without taking guitars with themselves. Derek Brooks (responsible for communication with artists) says that when Steve Lukather comes to the store selling their guitars, he knows that every guitar is tuned according to his standards.
Subsidiaries and trademarks:
Sterling by Music Man.
Brief history:
Forrest White and Tom Walker, two former employees of Fender, together with Leo Fender founded a company in 1972 in Fullerton, California, that two years later became known as the "Music Man". Initially, they produced mainly Walker's amplifiers, but in 1976 the instruments production followed. Two guitar players, the figures of which were intertwined in the big letter M, made up a "Music Man" logo.
When "CBS" bought from Leo Fender his company, the contract stipulated a restriction on deployment of a similar competitive business. It expired in 1975. In April the same year Leo was declared president of "Music Man Inc". The first guitar of the company in the middle of 1976 was "StingRay", presented together with the bass guitar of the same name. The instruments were made in a typical Fender style, but showed significant improvements in design and individual components. The models successfully applied the 3-screw mounting of the neck to the body, which earned a bad reputation when Fender did so - the company used this method in “the era of quality deterioration” which the company got enwrapped into in the 1970s.
"StingRay" with twin humbucker and fixed bridge followed the trends of its time, and as an option active electronics was offered. It wasn’t quite an ordinary instrument for Leo Fender's guitars, and a certain mistrust among guitar players to everything new ensued in quite a modest response. But Leo, as usual, didn’t see much sense in simply reproducing his past achievements, and sought to offer a real improvement in quality, harmony and performance.
Two years later the guitar "Saber" appeared with body outlines which were slightly different from "StingRay". It also had a large headstock with six pins in a row and neck from a single piece of maple, and as StingRay it was released in two versions - "I" and "II": "first" with a 12-inch neck radius and "jumbo" frets, "second" - with a "vintage" 7.5 inch radius and frets of standard size. Again there were neither single sensors nor vibrato, active electronics was already standard, as well as more thought-out circuitry and elaborate hardware. Despite these changes and a more solid image, "Saber" wasn’t too popular among musicians.
On the sidelines of the company’s activity, everything got completely unhealthy. The structure of the business was built in such a way that the instruments "Music Man" were produced by the Leo’s "CLF Research" brand, and when "Music Man" unsuccessfully tried to purchase it in 1978, Leo decided to secede and established his own guitar business company "G&L" in 1979. The first instrument under this new brand appeared in 1980.
A bit later "Music Man" continued to make instruments in Fullerton, but later got other production facilities involved, including "Jackson". Despite such confusion, a small set of models came out in 1980, when "StingRay" disappeared from the catalog, and the rest was released in the early 80's. In March 1984, "Music Man" was bought by Ernie Ball company, the production was moved to the north, closer to San Luis Odispo (California), where strings and accessories were produced, and the second chapter began in the history of "Music Man".
Until then, the basses of "Music Man" were more popular than guitars, so with the new owner the 4-string models were the first to go into production.
The prototype of the completely new model "Silhouette" was tested in 1986, and the production was started. This full-body Fender-style model was designed by former Valley Arts employee Dudley Gimpel with the support of country rock guitar player Albert Lee. But such elements as a stylish hewn body and headstock with the 4+2 pins solution were in line with the contemporary design of Music Man basses. As an option, a 24-fret maple neck with a rosewood or maple overlay, a fixed bridge or a tremolo bridge and various combinations of pickups were offered. The latest version was the Silhouette Special in 1995, its 22-fret neck and Wilkinson vibrato were the most obvious changes in a whole series of improvements to the basic model that is still being released. Ron Wood and Keith Richards are among the famous musicians playing the "Silhouette" - for them this choice of new, rather than time-tested vintage guitars was already a surprising exception.
Going back to the 1980s, we note that together with "Silhouette" the signature model of Steve Morse was produced in 1987. It incorporated an innovative 4-sensor configuration, preferred by the musician. A very popular Music Man model was a six-string EVH, which was being released during some years after 1991 – it was developed in close cooperation with the famous virtuoso Edward Van Halen. "EVH" was distinguished by the body of Van Halen's design, a special neck line and peculiar DiMarzio humbucker sensors. The original version with Floyd Rose vibrato soon was launched as an option with a fixed bridge, reflecting the changing demands of Van Halen. But in the mid-90s, the guitar player switched to cooperation with Peavey, which released a new signature model, so Music Man changed the name "EVH" to "Axis". Since then, the original "EVH", especially made of rare woods, has become a collectible. Prior to this, "Music Man" used the name "Axis" for a number of models-predecessors of Albert Lee signature guitar. One of these angular specimens, which earned the reputation of the first solid-body left-handed instrument of the new "Music Man", was made for Paul McCartney. Nigel Tufnel's remarkable model also had a more perfect version, featuring four pickups, a tachometer, and the name of notes on the inlay, apparently to increase the already dazzling speed of Tufnel.
Other models of the 90s in the guitar line made by Music Man were two more signature models, released in 1993 - "Luke" and "Albert Lee". "Luke" was made according to the specifications of Steve Lukather, and Albert Lee's guitar was distinguished by the angular shape of the body. In 1997, the budget version of "Axis" was launched - "Axis Sport" with two "MM90" sensors of the P-90 type - the first sensors manufactured by the brand. In 1999, "Music Man", following the fashion for combo guitars, put piezoelectric sensor onto the "Axis" (as an option).
Although Music Man doesn’t offer a rich selection, the company offers a high-quality, high-performance products which are among the best new generation guitars in USA.
Technical and technological achievements:
Sterling Ball, Ernie’s son and the current head of the company, is like no one else. He plays guitar and bass delightfully. He very carefully searches for an excellent sound, but at the same time he finds it funny to find something that is obscure or simply doesn’t exist. He likes to mess around with things, to ask questions, why they are arranged this or that way, and whether they can be improved. In addition, his life is closely connected to the major part of the history of electric guitar development. Sterling has been surrounded by all sorts of equipment since his birth. His father found a guy whose name was Leo Fender to find out all the possible things about Hawaiian guitars and new-fangled electric guitars that he was making. He also tested Fender's instruments.
Sterling, now 55, visited Leo’s factory when he was only 4, and by the time he graduated he had already got familiar to the whole factory. His father began to make a living by teaching the playing musical instruments, and also is believed to discover the first store of electric guitars in the country. Shortly thereafter, Ernie was the first to produce strings of special calibers, because the guitar accessories were still at the stage of formation back then.
As a child, Sterling packed strings and helped musicians find the things they needed in the store. Soon he began to go to the NAMM shows, perform not far from Los Angeles, presenting Ernie Ball company, control the sales and test the new Leo Fenders bass guitar called "StingRay" made by Music Man - Ernie bought it in 1984. A few months later, Dudley Gimpel came to the company. He was hired thanks to his "six-string" curriculum vitae – thanks to the Telecaster-like guitar - showing his ability as a guitar master. Since then, Sterling and Gimpel have been working together. It's impossible to discuss the strings made by Ernie Ball in Coachella, not mentioning Ernie Ball himself, and Ernie Ball Music Man instruments made in San Luis Obispo, California, can’t be discussed without mentioning the role of Gimpel in designing company’s products. Go sightseeing to the storehouse of prototypes and serial models - Gimpel can tell about any nuance of the specification, any which can only come to your mind, right up to exact dates and millimeters - because he used to make units, manage production and disassemble instruments. He can explain the location of the magnets in the Old Smoothie guitar pickup - the first guitar "StingRay" that Leo made in 1976 and why the prototype No. 19 of Eddie Van Halen's signature guitar is equipped with the "Floyd Rose" tremolo by Schaller. Gimpel could tell you everything you wanted to know about the equipment of Ernie Ball Music Man.
Although the connection of Ernie Ball Music Man with Leo Fender is significant, and in some cases directly indicates the source of inspiration, it can in no way be decisive. In a fairly conservative industry represented by many companies, the shape of guitars, electronics and sound for almost 50 years haven’t changed much - the company EBMM was able to occupy its niche balancing between something traditional and something new. For example, although the company is proud of the fact that the guitar "StingRay" brought it fame, but all the same it continues to break away from the usual, releasing such guitars as, for example, the bass "Bongo". "Bongo" appeared in 2003, and now it is available in three versions: with one humbucker, with two humbuckers, with a humbucker and a single (optionally also with neodymium magnets in pickups and/or a piezo pickup integrated in the bridge), as well as 18v 4-band (for two pickups) or a 3-band active equalizer. As for guitars, some quite traditional examples have won the love of many guitar players around the world, but the company itself is into some new models of 2011, which are very innovative.
As for the way how guitars and bass guitars are made: 50 to 100 instruments that the factory produces daily in San Luis Obispo, show excellent and harmonious operation of automated machines and careful and accurate manual labor of dozens of people working diligently so that each instrument would make any musician happy. Despite the supply of guitars to 86 countries, the company Ernie Ball Music Man still works as a small factory: the stock of production isn’t harvested - the instruments can be only ordered by customers and dealers.
Standing between an automated grinding machine and an employee with 26 years of experience polishing those places that the machine can’t do, Sterling says that you can understand where automatic work is required, and where the manual approach is necessary – it animates the guitars a little.
One of the secrets of the famous guitar necks made by Ernie Ball Music Man is their deliberate deformation after the overlay was attached. The necks is stretched to achieve a 0.007-0.008” bend. Then this bend is removed using a belt-grinding machine, bringing the overlay to the required radius. And then the neck is weakened. Maybe someone will disagree with such a decision, but for a company known for the quality of its necks, it only contributes to the individuality. Other features include impregnating the necks with oil and coating them with wax (everything started with the Eddie Van Halen’s guitar, now it's a standard feature for many models) and a "roasted" neck (this gives the maple an attractive brown hue - the neck looks like a cookie – especially if it’s a bird's-eye maple kind of wood).
Interesting technological features of guitars and bass guitars production by Ernie Ball Music Man:
Binding. Instead of gluing and rolling plastic rim, it is poured into a mold mounted on the body to precisely match the "anatomical features" of each guitar.
Frets. Plek machines for embedding the frets are not used. The processing of the frets takes about 45 minutes, and the frets themselves cut in such a way that there is a gap on each side of the neck, thus, no pruning is required. This gap is then manually filled with varnish and sealed.
Take care of the guitar body! To the place the neck is fixed, the temporary handle is attached, which is then clamped in the vice on each table, so that the body is in a "suspended" state, while electronics are placed in it. This protects the body from scratches and damage from screws, tools and debris located on the tables.
Wood processing. Despite the fact that the company buys already dried and processed wood, it is still used in the factory for drying (not ultraviolet drying) to draw more water from the wood. It takes 4 days to fully “mature” the guitar body.
Cavities are striped. Guitars "Reflex" have cavities in the body in the form of parallel grooves.
Sterling completely adopts an "innovative and special" approach in creating guitars and basses. That’s proven by the fact that he gets surprised that after the purchase it is still necessary to adjust the guitars. He is also annoyed by the fact that musicians are too slow in accepting innovations. He says that it would be nice to improve the guitars a bit, you can implement many technological solutions, the challenge is to come up with better ways of making new, more convenient instruments.